
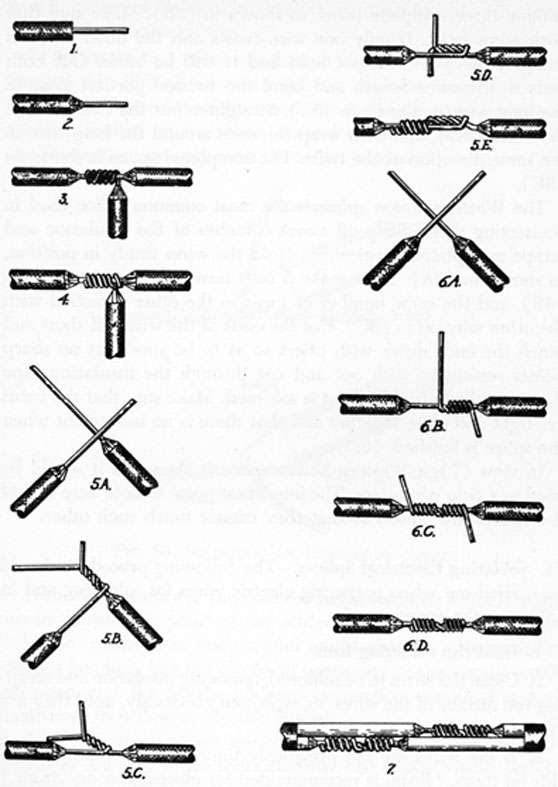
It is always a good idea to cover the terminated ends of your automotive wire with some heat shrink tubing. Basically, if you crimp your wire and terminal together, and you cannot pull them apart, the connection will most likely suffice. The key is to make sure that there is good electrical contact between the copper strands of the wire, and the barrel of the terminal or connector. However, in 95% and more cases, a good crimp will work just as well. Is it better to solder or to crimp connectors to automotive wire? Soldering is superior since it creates a maximum amount of surface contact between the wire and the terminal or connector. The voltage reading on your volt meter at the end of the wire will only be 9.6 volts, and the wire is absorbing a whopping 48 watts of power! Now let’s say your wire has a 20% voltage drop. If you are running 20 amps through your wire then your wire is absorbing 4.8 watts of power. So if you put a volt meter on your battery and read 12 volts, when you put your volt meter on the end of the wire, you will read 11.76 volts. That leaves 11.76 volts, or units of work left. If you’re wire has a 2% voltage drop, then the wire is using up 0.24 volts, or units of work. In its simplest terms, you can think of 12 Volts as during 12 units of work. This lost energy is realized in the form of a voltage drop at the end of the wire. Why is the size of an automotive wire so important? When electricity passes through a wire, The wire resists the electricity and some of it is converted into heat that is absorbed by the wire. Based on the chart above, you would want to use 12 gauge automotive wire for your floodlights. The length the wire needs to be to connect to the floodlights is 9 ft. For example, you want to add some flood lights to your vehicle. In order for your automotive electrical system to perform properly, your wire must be sized properly based on the amount of current (amperage) the wire must carry, and the length that the wire needs to be.
